Analyzing Margin Drivers for Manufacturing Complex Goods
Manufacturing
D&A Solutions
It’s become frighteningly simple to identify which single component from thousands is affecting profitability—letting us take action before it grows into a problem.
Director, Sales, Inventory & Operations Planning
Meeting the Challenge
How can a Finance team understand the factors driving margin in manufacturing complex goods?
The Finance team at our client, a major global automotive supplier, was hungry for deeper insight to understand cost fluctuations in their manufacturing costs across their catalog of finished goods. But even a basic analysis was difficult, since it could be done only for a single component at a time. Considering that the company’s finished goods are automotive systems composed of a complex web of hundreds or thousands of components—both hardware and software—it was simply impractical to conduct a thorough investigation of the reasons costs may have increased for a particular finished good by reviewing each individual component.
Another challenge was understanding the different drivers of increased costs. Sometimes a part was simply more expensive, or had different pricing terms, shipping changes, or needed to be sourced from a new supplier because of scarcity. But other factors also contributed. With global sourcing, currency fluctuations can have a major impact on pricing. And with the complexity of the company’s product catalog, any modification to a Bill of Materials will also influence cost. But there was no easy way to identify the reasons cost increased for a finished good composed of dozens or hundreds of components.
Our Solution
Axis designed a solution that exposed the true margin drivers in complex goods manufacture
Axis worked closely with the company’s Finance team to identify the various drivers that impact pricing, including an in-depth analysis of existing data, to design the right approach.
Our solution lets the company analyze the underlying reasons why costs fluctuated for any component in any finished good, and how much those fluctuations contributed to the net change over time. Now, the team can understand not only the drivers of cost changes, but how much each driver contributed to the change in margin.
So for a given finished good, a change in margin may be 30% attributable to higher component prices, 20% to changes in the bill of materials and the choice of materials used, and 50% from currency fluctuations. With that kind of detail readily at hand, the finance team has the tools it needs to conduct deep margin analysis.
With the help of Axis, the Finance team now has a central platform to identify the top influencers and main drivers for cost fluctuations, with an easy-to-use interface requiring no SAP expertise to analyze. They can evaluate performance-based metrics (sales, cost, margin; total or per unit) from the company level down to the level of BOM components, including currency variations. The company can also more easily negotiate with suppliers, identify multi-sourcing opportunities, and justify price increases in its products to maintain or improve margin levels.
Solution Sample: By “exploding” a Bill of Materials down to its component parts and marrying them with SAP pricing data, finance managers can quickly identify the underlying causes of lower margin, such as higher component prices or increased shipping costs.
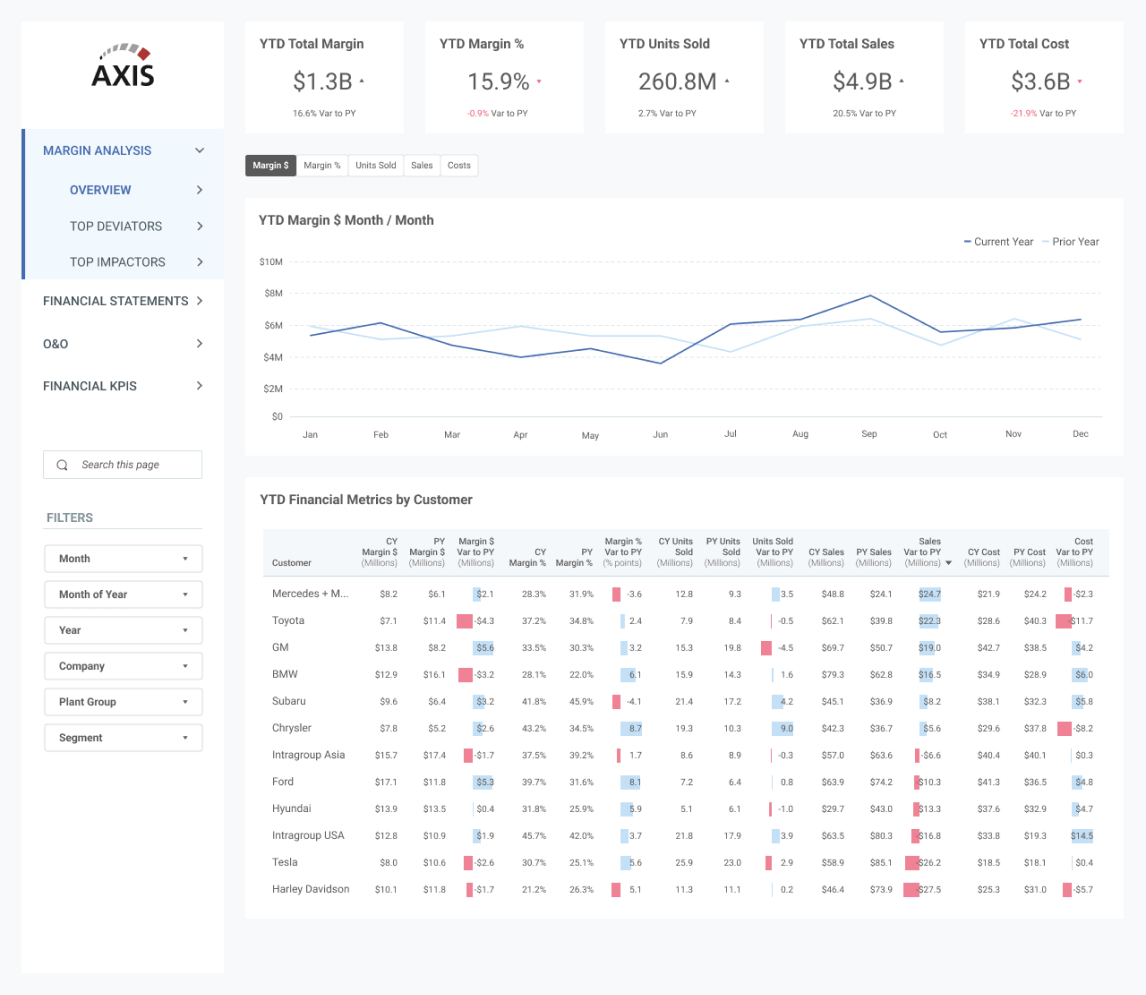
Are you ready to take the next step on your Data & Analytics journey?