Accelerating demand planning with real-time supply chain insights
Manufacturing
D&A Solutions
Demand planning for just a few products used to take a team of people at least a week. Now one person can plan for an entire category in a few minutes. The Demand Cube helps head off supply chain shortages before they happen to keep our customers happy.
Senior Manager, Supply Chain Constraints
Meeting the Challenge
How can supply chain managers better plan around supply chain disruptions?
Demand Planning has always been a vital part of maintaining a company’s competitive edge. Without an accurate, comprehensive and timely view balancing demand estimates against component supply and inventory, Sales, Inventory & Operations planning (SIOP) professionals often have to make best estimates based on their instincts. And when a company has to balance demand for complex finished goods against a fluctuating supply of thousands of components, SIOP’s job becomes that much more difficult to do well.
That’s the position our client, a Fortune 100 manufacturer of finished consumer electronics, found itself in. For years, the company struggled to integrate data about the finished goods it sells with the complex web of components they use to build them. A manual (and error-prone) process, exporting data from multiple systems into spreadsheets, it often took weeks to get a snapshot of the current supply chain for even a small set of finished goods—by which time the report was already out of date. Considering they make hundreds of SKUs composed of tens of thousands of components in millions of combinations, the company’s approach was just not sustainable or scalable.
Then in 2020, just before the global pandemic created new disruptions and risks in the global supply chain, they called Axis.
Our Solution
Axis designed a Demand Cube that unifies demand, supply and inventory
After using our Solution Design Methodology to learn about the SIOP team’s needs and the data sources they relied on, Axis worked up prototype designs for a “Demand Cube”—an application that brings together the three dimensions the company needed to plan: demand for finished goods, supply of component parts, and on-hand inventory. After several design iterations, we constructed data pipelines and a front-end application that we tested with users to make sure it met their needs.
For the first time, the Demand Cube provides a comprehensive view into all of our customer’s supply, demand and inventory data and finally lets them plan finished goods production in near real-time, while freeing up resources for more valuable work. Now, our customer can compare daily demand for finished goods against suppliers’ commitments for the parts in a Bill of Materials that are needed, so they can decide what goods they can manufacture at any given time, and when they can be ready for delivery.
Inventory data is now aligned with finished goods and components to help avoid inventory shortages.
The SIOP team is quickly alerted to material shortages at a plant, customer and supplier level, and can inspect how variances will impact finished good production. Of course, this also helps plant managers and procurement in planning and inventory control.
The component inventory can be compared to order requirements to estimate when components will be exhausted—information critical to know at all times, but especially useful during stressful periods such as the recent pandemic.
As a beneficial side effect, our customer now gets historical visibility into changes in finished goods orders over time to help identify shortage trends.
When the COVID-19 pandemic bore down on global supply chains, the Demand Cube we designed proved invaluable to help our customer minimize disruption of its supply chain. With near real-time information on supply, demand and inventory, they were able to quickly adjust production and find alternate suppliers.
And because the Demand Cube enables a timely and comprehensive view of the supply chain, it has since found new audiences around the company, where it’s been extended and adopted by other teams. Plant managers use it to help plan capacity and schedule production; engineers can better plan new product development; buyers get new insights into lead times; and the sales and marketing teams can better set customer expectations.
Solution Sample: The executive dashboard provides a graphical view comparing data sets to quickly identify current and potential shortages of materials at a plant, customer and supplier level.
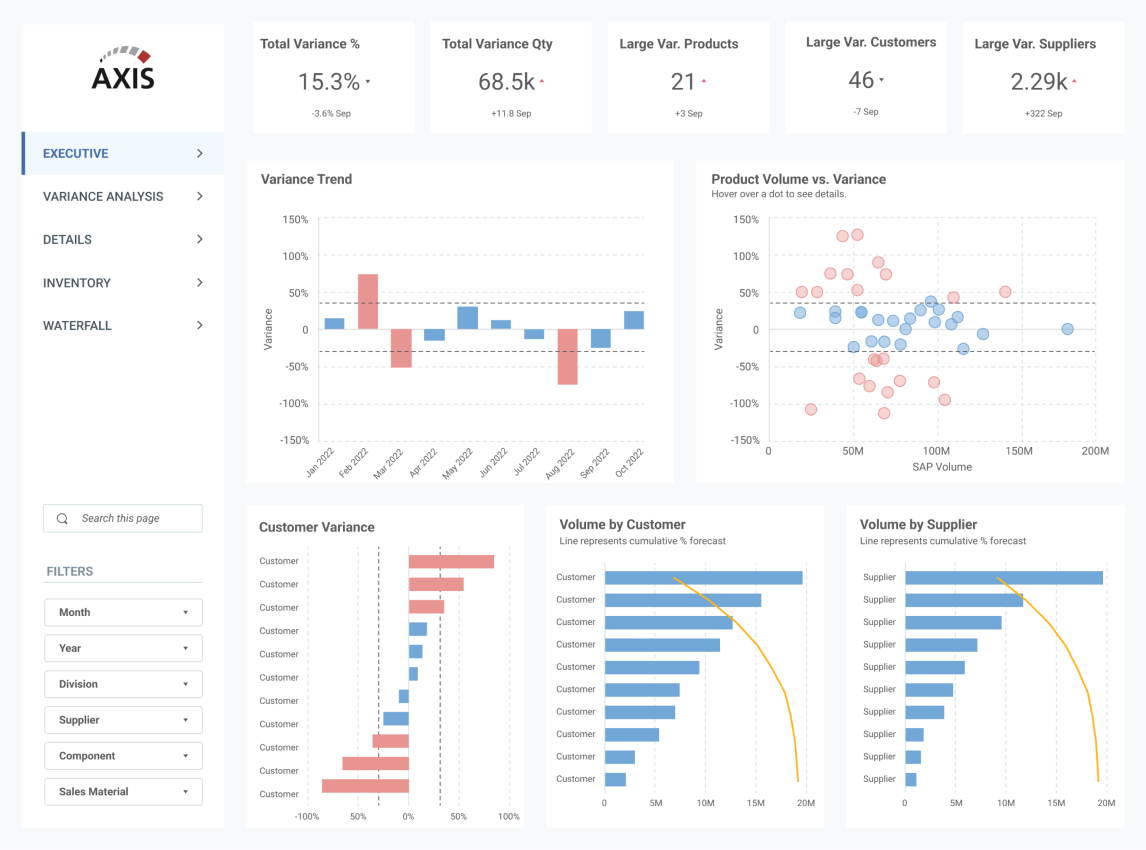
Are you ready to take the next step on your Data & Analytics journey?